Mastering Injection Molding: What Every Manufacturer Should Know
Injection molding is a crucial manufacturing process that shapes a wide array of products, from simple household items to complex automotive components. It involves injecting molten material into a mold, where it cools and solidifies into the desired shape. This technique is not only efficient but also allows for high levels of precision and repeatability, making it a favorite among manufacturers worldwide. Understanding the intricacies of injection molding is essential for any producer looking to optimize production and ensure the quality of their products.
At its core, the injection molding process consists of several key stages, including material preparation, injection, cooling, and mold ejection. Each step plays a significant role in determining the final product's quality and performance. With advancements in technology and materials, manufacturers can now explore various techniques and innovations within injection molding that can further enhance their operations. In this article, we will delve into the essential aspects of injection molding processes that every manufacturer should know to stay competitive in the ever-evolving market.
Understanding Injection Molding Process
Injection molding is a manufacturing process used for producing parts by injecting molten material into a mold. It is widely adopted in industries such as automotive, consumer goods, and medical devices due to its efficiency and ability to create complex shapes. The process begins with the heating of thermoplastic or thermosetting plastic pellets until they melt and become a viscous liquid. This liquid is then injected into a pre-made mold cavity under high pressure, allowing it to fill the space and take the shape of the mold.
Once the mold is filled, the material is allowed to cool and solidify, forming a solid part. The cooling time can vary depending on the material and the size of the part, but it is a critical step that impacts the quality and dimensional accuracy of the finished product. After cooling, the mold opens, and the newly formed part is ejected, ready for any secondary processes such as trimming, machining, or assembly. This entire cycle can be completed in a matter of seconds to minutes, making injection molding a highly efficient process for large-scale production.
Maintaining precision in the injection molding process involves careful monitoring of several factors, including temperature, pressure, and cooling times. Control over these variables ensures that the resulting parts have consistent quality and meet the required specifications. Advances in technology, including computerized controls and sophisticated mold designs, have further enhanced the accuracy and repeatability of injection molding, making it a go-to solution for manufacturers looking to optimize production time and minimize waste.
Key Considerations for Manufacturers
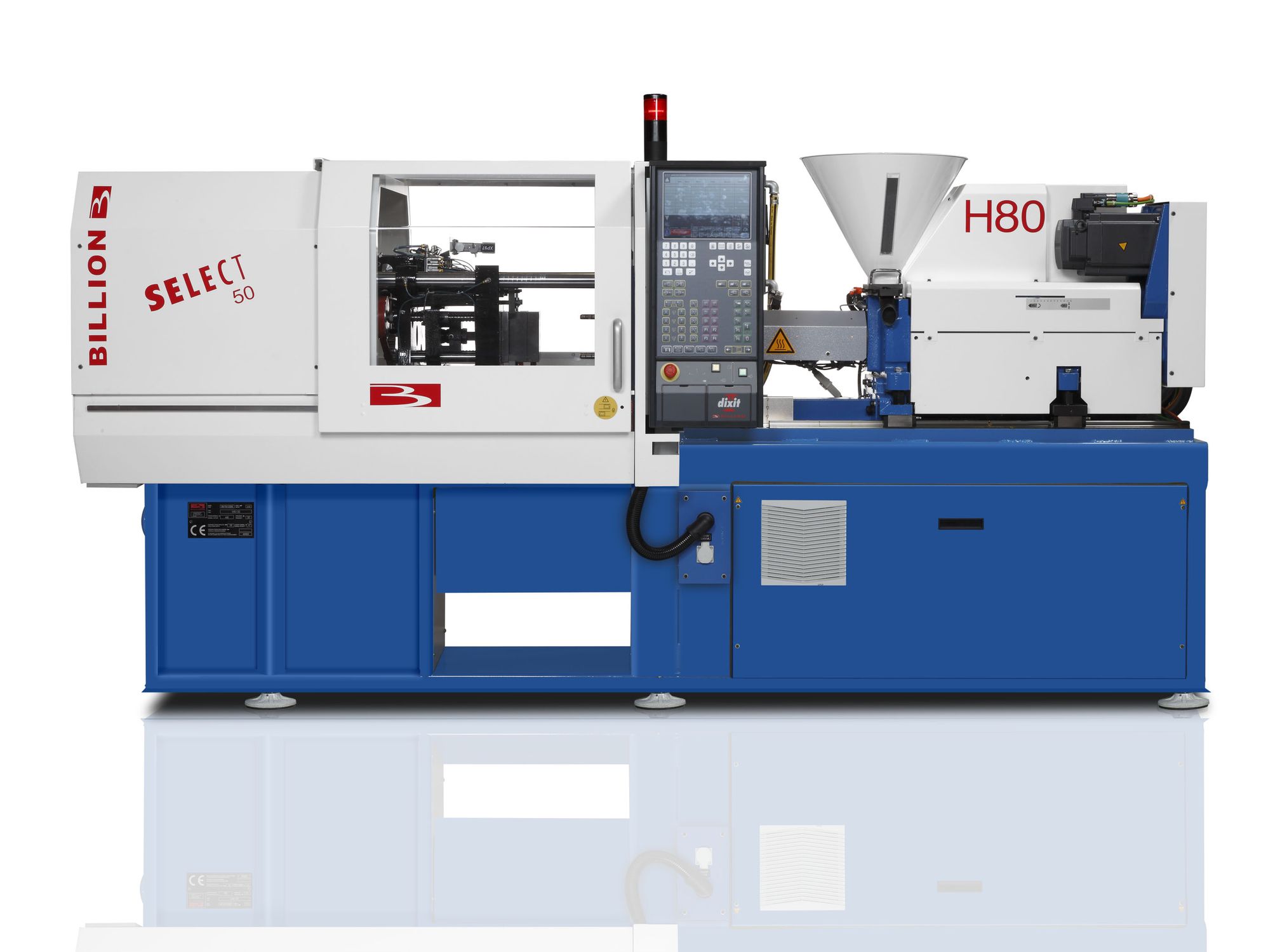
When engaging in injection molding, manufacturers must first evaluate the material selection. The choice of plastic resin significantly affects the quality, durability, and functionality of the final product. Common materials include thermoplastics like ABS, polycarbonate, and polyethylene, each offering unique properties. Manufacturers should analyze the specific requirements of the product, such as strength, flexibility, and heat resistance, to ensure optimal performance.
Another critical aspect is the design of the mold itself. A well-designed mold can greatly improve the efficiency of the injection molding process and reduce production costs. Factors such as wall thickness, draft angles, and gate locations must be carefully considered to facilitate proper filling and to avoid defects. Collaboration with experienced mold designers can lead to innovations that enhance productivity and product quality.
Finally, understanding the importance of cycle time and production efficiency is vital for manufacturers. Optimizing these elements can lead to significant cost savings and quicker turnaround times. By fine-tuning parameters such as inject speed, cooling time, and pressure ratings, manufacturers can achieve a more streamlined process. Continuous monitoring and adjustments will ensure that production remains competitive while maintaining high standards for safety and quality.
Common Challenges and Solutions
Injection molding is a sophisticated process that can present various challenges during production. One common issue is inconsistent part quality, which can lead to variations in strength, dimension, and surface finish. This challenge often arises from fluctuations in material temperature, pressure, or cycle time. To address this, manufacturers should invest in precise temperature control systems and regularly calibrate their injection molding machines. Implementing statistical process control can also help monitor the production process and maintain consistency.
Another challenge faced in injection molding is material wastage due to excess scrap. This problem often results from improper gating design or incorrect machine settings. To reduce waste, manufacturers can analyze and optimize the part design to improve gate location and size, ensuring efficient material flow. Additionally, using simulation software can help predict the best design before tooling, minimizing the risk of excessive scrap during production.
Lastly, machine downtime can significantly impact productivity and profits. Common causes include mechanical failures or the need for mold changes. To minimize downtime, manufacturers can adopt a proactive maintenance schedule and invest in training for operators to quickly address minor issues. Implementing a robust inventory management system for spare parts can ensure that essential components are readily available, reducing the wait time for repairs and keeping production on track.